Overview

Efficient adhesive application is vital for the manufacturing of EV battery packs, ensuring structural integrity and operational safety. A leading EV battery pack manufacturer faced significant challenges in bonding cylindrical cells to cell holders in EV battery module assembly due to inefficiencies involved in traditional gluing methods. The ADoST SDS PRO, semi-automatic silicone sealant dispensing system addressed these challenges, offering precision, efficiency, and improved ergonomics.
Industry background

EV battery production demands high precision, especially during sealant application on cell holders in EV battery module. This precision ensures the reliability, durability, and performance of battery packs. Hand operated applicators such as pneumatic dispensers, often fall short due to operator fatigue, inconsistent adhesive application, and material wastage leading to large work in process and high cost. This is exactly the situation our customer found itself facing every day on the shop floor.
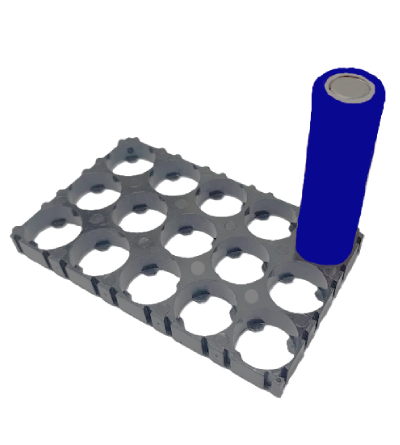
Cylindrical Cell Holders
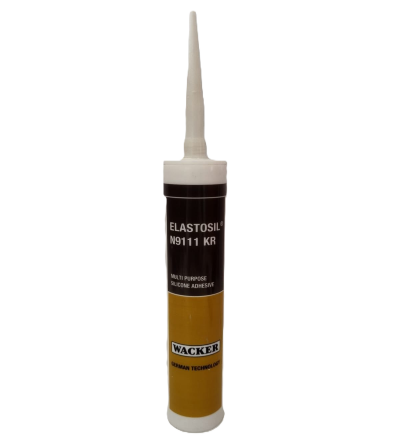
1K Sealant Cartridge 300ml
The Challenge

The workers had to apply RTV Silicone Sealant in nearly 33,600 spots daily across top and bottom cell holder of 350 module assemblies. This was achieved using a 300ml manual pneumatic cartridge dispenser. This repetitive task caused hand fatigue, errors, and operational inefficiencies. Furthermore, the large-diameter dispense nozzle lacked the precision required to apply sealant accurately to the designated locations. It resulted in oversized beads, leading to adhesive waste and compromising application quality. The situation required an innovative dispensing solution to enhance precision, reduce waste, and improve operator well-being.
ADoST’s Solution

The manufacturer turned to the ADoST team, who quickly got to work understanding their requirements. In response, ADoST proposed the SDS PRO, a semi-automatic dispensing system to tackle their unique challenges.
This innovative system was a game-changer. Instead of operators holding a cumbersome pneumatic dispenser, the 300ml adhesive cartridge was mounted on a stationary tower. Operators now handle a lightweight dispensing pen, designed for enhanced manoeuvrability and precision.
Dispensing parameters are controlled through an advanced HMI unit that also offers purge feature to ensure the dispensing tube does not clog during lunch or shift break.
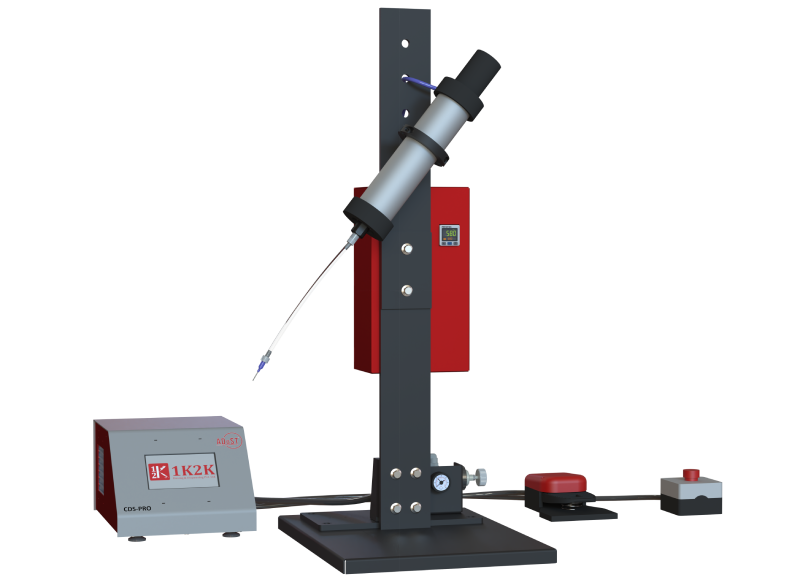
ADoST SDS Pro Dispenser
Customer Experience

The implementation of the SDS PRO quickly transformed daily operations for the EV battery pack manufacturer. The customer observed precise and uniform adhesive application across all spots in cell holder with minimal variation. The lightweight pen allowed operators to work comfortably, significantly reducing fatigue. Material consumption dropped as bead sizes were optimized, cutting waste by a substantial margin. These improvements also streamlined production, increasing throughput and lowering overall cycle times.
Conclusion

The ADoST SDS PRO transformed the customer’s sealant application process, improving productivity and quality while reducing material waste and worker fatigue. Inspired by the results, the customer has expanded its use across all production lines in their facilities, solidifying ADoST’s position as the leading manufacturer of adhesive and sealant dispensing.