Industry background

A leading manufacturer of automotive fluid transfer hoses aimed to enhance the consistency in the dispensing of Cyanoacrylate adhesive (Loxeal 43S) to bond EPDM hose and Steel clamps.
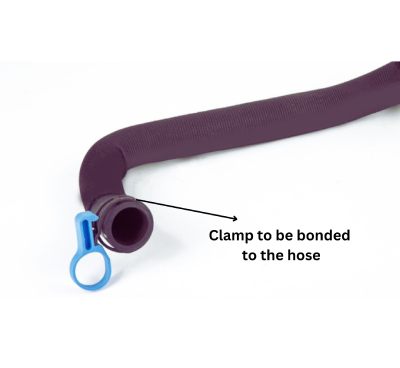
Final assembly
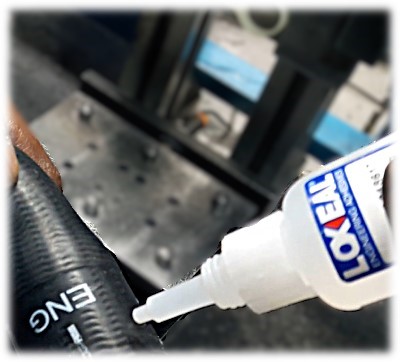
Manual adhesive dispensing

20gm adhesive bottle
The customer was initially using 20gm bottles of Loxeal 43S and was manually applying the adhesive on the hose by hand pressing the bottles. While this application method was good enough for low volume production, it became a major bottleneck when the production volumes increased. High glue consumption and low production speed posed frequent challenges in their scaling up efforts leading to management dis-satisfaction. Even at the best of times the production never crossed 1100 units a shift while consumption per part stayed about 0.05gm.
Customer tried implementing Cyanoacrylate dispensing machine from one of the globally leading manufacturers but inconsistent performance and frequent Valve clogging forced them to revert to manual application.
Understanding the Problem

ADoST application team during one of their early sales meetings got to understand that customer was looking for a dispensing system that could operate non-stop for days without tube or valve clogging. They were keen that the machine could provide consistent drop size through-out keeping per part consumption predictable and sustainable.
ADoST Solution

ADoST application team proposed testing ADoST PPS NXT, a next generation Cyanoacrylate dispenser that incorporates a highly engineered precision pinch valve that does not come in direct contact with the Cyanoacrylate glue thus eliminating frequent clogging of valve experienced in traditional diaphragm valves and syringe dispensers.
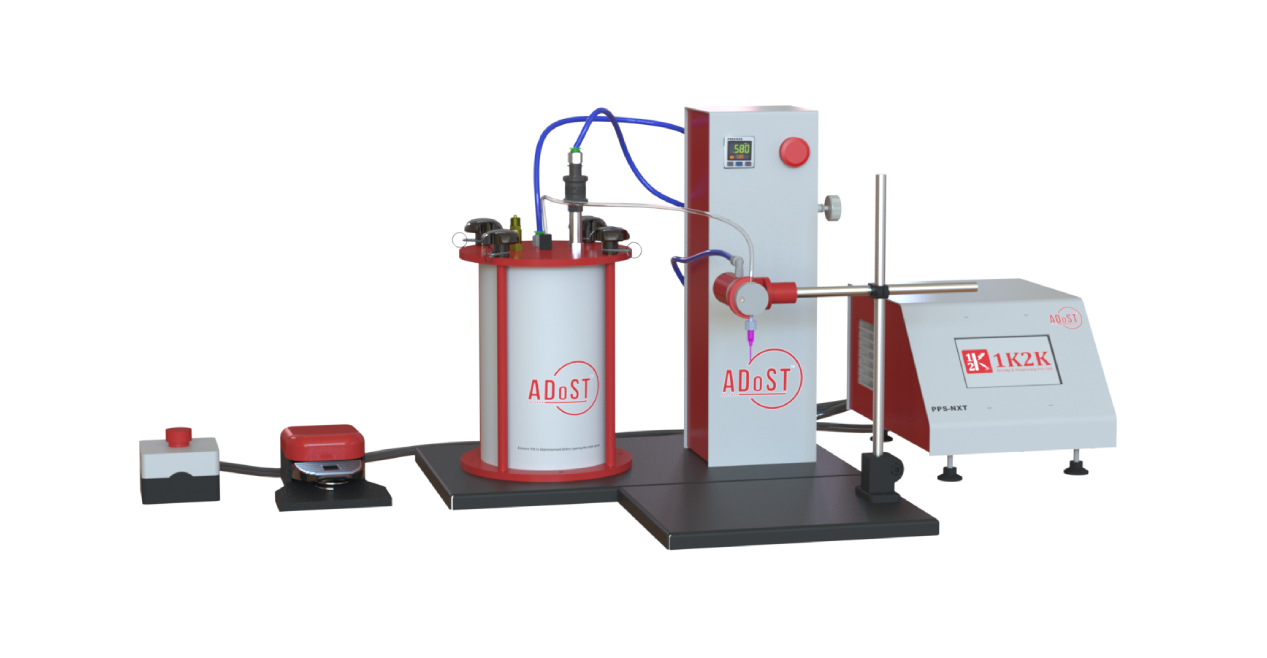
In addition to minimal wet parts, ADoST PPS NXT can be fully controlled though an interactive digital controller that makes this machine easier and extremely reliable to operate and use on high speed assembly line.
Customer Experience

During tests customer observed that ADoST PPS NXT’s operating principal and highly engineered manufacturing techniques enabled them to run continuous production for days without any change of tube, part replacement or valve cleaning. Per part adhesive consumption could be optimized with consistent drop size all the way. The pressure pot system of ADoST PPS NXT allowed customer to move to a larger pack of adhesive bottle that itself saved over 15% of the glue cost.
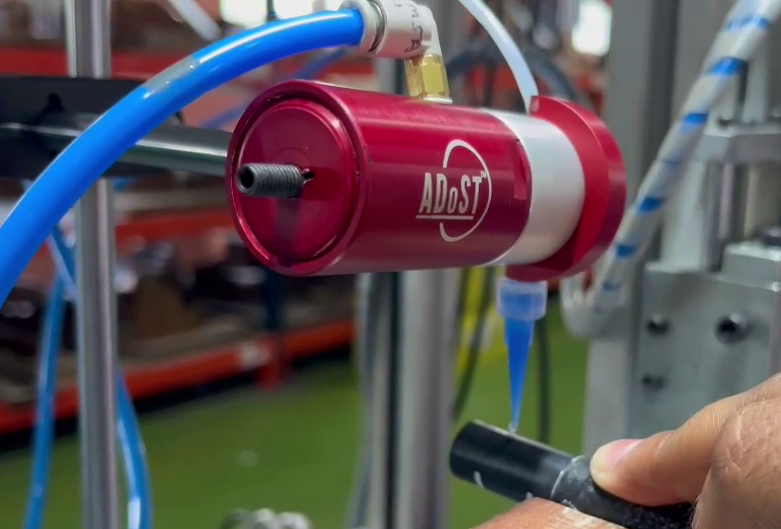
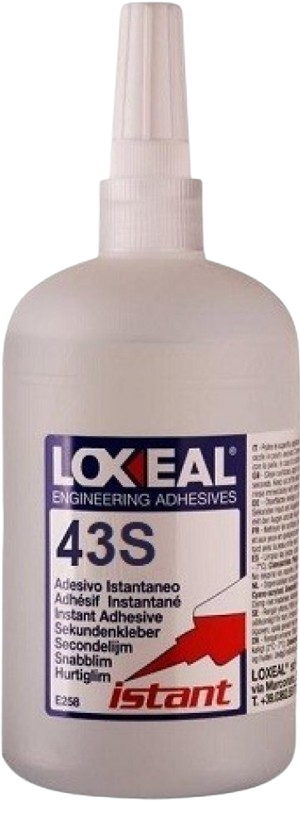
Large bottle for ADoST Pressure Pot
Customer Benefits

In addition to consistent and sustainable drop size and the fact that the machine needed no consumable change for extended time period, following direct benefits were observed:
Application Method | Adhesive Pack Size | Glue Consumption/Part | Glue Cost/Part-₹ | Production/Shift |
Previous method | 20gm | 0.03gm | 0.63 | 1100 |
ADoST method | 500gm | 0.02gm | 0.32 | 1600 |
Conclusion

As on the date of writing this Case Study, ADoST PPS NXT has been already successfully operating continuously for over few months at this assembly line and based on their experience so far, customer is already exploring setting up a new ADoST in their upcoming project.